When making crane wheels there are two main factors of the product that can affect its lifecycle. Surface hardness and depth of hardness. Both factors correlate to data provided in crane manufacturing tables of loading for crane wheels. These tables provide the maximum loading condition for a wheel diameter based on rail size and optimum conditions. These factors are calculated and compared to a material’s hoop stress (wheels ability to withstand being crushed) to ensure that spalling will be minimized. Over time and real world conditions, any material can become prone to spalling after significant wear has occurred on the wheel. Most vendors will do their best to extend the lifecycle of there products as much as possible.
Some competitors use either AISI 1045 or AISI 1055 cast or forged wheel and then place it into a carburizing furnace. For 1045 or 1055, the selected temperature would be either 871°C (1600°F) or 899°C (1650°F). Case hardening (carburizing) at these temperatures only affects the first 0.08” of the wheel. If a higher temperature is used for this steel, the grain structure of the material could be detrimentally affected, which will be explained in a later blog post. Too large of a grain structure combined with a shallow depth of hardness can lead to spalling which is a common failure mode seen in crane wheels. At McKee’s Rocks we offer AISI 1070 M forged steel for all standard duty crane wheels, which due to the modified chemistry allows for a higher depth of hardness. Our process of flame hardening the wheels involves heating the wheel to a selective tempurature at the rim area and then quenching the wheel to “set” the hardness. The table shown compares the typical hardness values in Rockwell and depth through the wheel. Standard 1045 and 1055 carburized material does not have the hardenability of our 1070 modified chemistry. Our alloy has a greater depth of hardness. When carburizing the surface the carbon content for a 1045 or 1055, the initial hardness is higher but will taper off quickly and can go below the required hardness at the depth required.
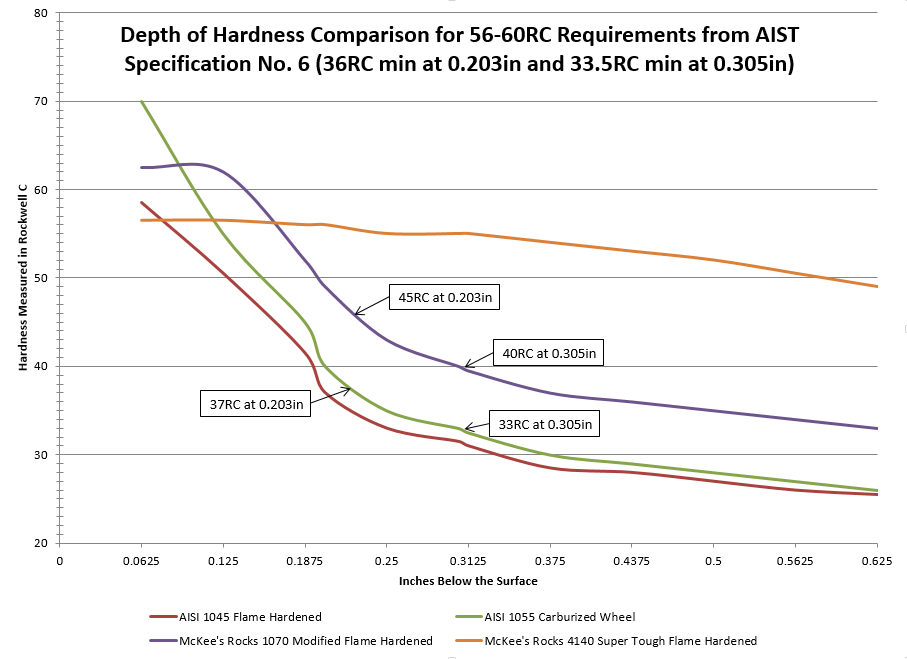
Customers have also asked for wheels that will withstand more rigorous conditions and duty cycles, therefore we also offer 4140 steel wheels with a flame hardened treatment that allows a through hardening to occur due to the alloy content of the steel. This alloy is shown as well to provide a baseline for carbon steels vs. alloys and the benefits that can be gained from the added alloys. We at Mckee’s Rocks Forgings have always endeavored to supply the best possible wheels we can provide our customers and will continue to do so.